Acoustic design
The development of complex enginering structures with given vibroacoustic characteristics (acoustic design) requires the elaboration of calculation technologies for their design and methods for their testing. The urgency of this problem, e.g., for ships and aircrafts is due to the high cost of design errors, while the complexity of the problem is caused by the need of rapid analysis of the design options that best match the actual conditions of operation and rigid requirements to the prediction accuracy.
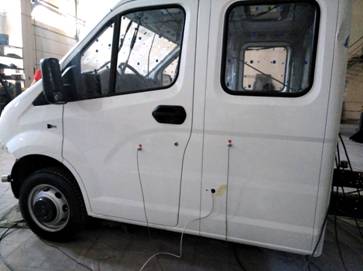
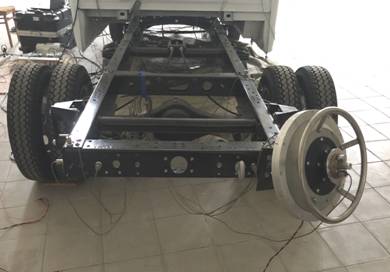
An approach combining the scale physical modeling, the development of numerical finite-element models (FEM), and their experimental verification has been developed at the IAP RAS. In designing, a numerical model of the prototype is created by preliminary drawings, which allows a detailed study of vibroacoustic characteristics of the system for various structural concepts; and a physical geometrically similar model is manufactured in a given scale ratio, which provides the obtaining of field measurement data; fine tuning of the model parameters, and test of its recommendations. The result is a high degree of the prediction compliance with the characteristics of the actual system before it appears in full scale.
To provide a technological cycle of the acoustic design, several measurement techniques were developed and adopted, the instrumental and test bases were created, a high level of the computing power was supported, and the algorithms and software for the numerical analysis were improved, namely:
- the reciprocity method was used to study the coefficients of variable force transfer to the external field, the frequencies and acoustically active mode shapes, and the efficiency of the employed facilities of acoustic protection;
- a set of vibration sensors, hydrophones, and vibrators with data collection and excitation control was developed to test a model with about 500 measuring channels;
- a computer cluster of 256 processors for the numerical experiments on the FEM with several tens of million units was adopted;
- an algorithm for the superelement computing was found to accelerate the calculations of design options.
The use of new calculation algorithms has enabled one to significantly increase the acoustic design capabilities and hence to successfully meet the challenges of acoustic optimization of the constructions relative to mixed acoustic and strength criteria with allowance for the plastic deformation, which is important for objects with extreme dynamic and static loads. According to the experimental verification, the calculation methods are suitable in accuracy for determining the target strength of elastic bodies with arbitrary geometry and internal structure. In particular, it is possible to detect the effect of the hull resonances of an object and its internal structure on the scattering cross section.
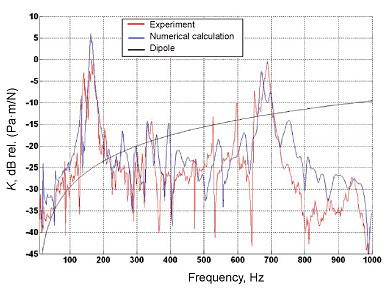
The numerical simulation technique developed at the IAP RAS permits direct numerical simulation without the approximations related to the peculiarities of scaling, vibration and acoustic fields in the natural objects in a fairly wide frequency range.
The resulting accuracy of the finite-element models enables one to use them not only for calculating the radiation level, but also for solving the inverse problems when the measurement results are taken as the initial data:
- in searching for vibro-active sources by the phase conjugation method modified for the vibration field (P.I. Korotin);
- in determining the contribution of individual mechanisms to the total field of the structure, if there are signals from extraneous sources (A.S. Suvorov, P.V. Artelny).
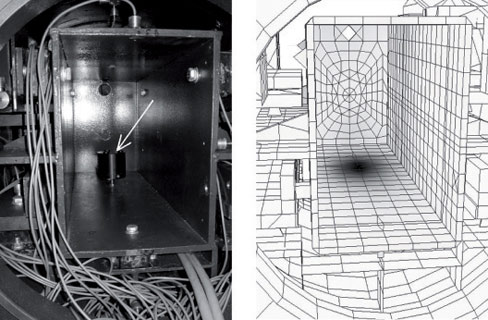